As plastic waste piles up and recycling rates remain disturbingly low, policymakers and researchers are exploring alternatives to manage the problem. A discussion paper by KAPSARC researchers Julio Arboleda and Evar Umeozor examines the potential of plastic-to-oil technology as a possible answer to the crisis, with a focus on Saudi Arabia’s waste management landscape.
According to the OECD Global Plastic Outlook, global plastic waste production reached a massive 353.3 million tons in 2019, yet only 9% was recycled. The United States was the world’s largest producer of plastic waste, followed by China. At the same time, the United States had one of the lowest recycling rates at just 4%. Even Europe, with advanced recycling technologies, recycles only 14%. In the Middle East and North Africa, the recycling rate stood at 5%.
Although there is no official data on plastic waste in Saudi Arabia, the country generated an estimated annual average of about 53 million metric tons (MMT) of garbage during the past decade, with plastic accounting for 10-15%. A staggering 95% of this waste ends up in landfills or is disposed of untreated in the environment, with only 5% recycled.
However, Saudi Arabia has ambitious plans: by 2035, the Kingdom aims to process more than 106 MMT of waste annually, with a 42% recycled and 19% designated for energy generation through incineration.
To achieve these goals, innovative processes and waste management systems will need to be developed. Plastic-to-oil is one such technology with the potential to make a significant impact. While not a comprehensive fix, it can play a valuable role in reducing environmental pollution when combined with other initiatives. More importantly, plastic-to-oil technology has the potential to create a profitable market for recycled plastic waste, encouraging recycling on a larger scale in many countries.
“While plastic-to-oil technology is not a silver bullet, its ability to generate value from waste makes it an important tool in the broader effort to tackle the global plastic crisis.”
Julio Arboleda
“The concept of the ‘plastic bank’ or money for plastic is one of the most attractive methods for increasing plastic recycling,” says Arboleda. “Converting plastic to energy, specifically plastic to oil, is one way of doing this, especially if oil prices can cover production costs.”
Another advantage of plastic-to-oil, particularly through pyrolysis, is its relative maturity compared to alternatives such as the use of nanocellulose to accelerate biodegradation of polymers or genetic methods to increase the production of bioplastics, which are in early stages of development.
The authors believe it could be one of many solutions to treat critical levels of accumulated plastic waste.
Promise vs. reality
Despite the promise it offers, plastic-to-oil technology faces several challenges before it is accepted, notes Arboleda. “These include the cost of the process; the generation of toxic side products; the uncertainty of plastic waste as feedstock; and a lack of consensus about the greenhouse gas emissions benefits of pyrolysis oil production.”
Additionally, plastic-to-oil conversion is still an emerging technology, with a limited number of suppliers providing the specialized pyrolysis systems required. However, by 2024, some projects employing plastic-to-oil technologies were already operational, demonstrating profitability and success.
One of the biggest challenges for producers remains securing a consistent and reliable supply of standard-quality plastic waste. This highlights the need for a sustained, well-organized recycling infrastructure to support the industry. Most of the successful pilot plants are in countries with advanced recycling programs, such as Austria and Norway, which demonstrate the feasibility of plastic-to-oil conversion under controlled conditions.
In Saudi Arabia, SABIC in collaboration with ARAMCO and TotalEnergies has already launched the first processing plastic waste to oil plant at scale in the MENA region.
Like many emerging technologies, converting plastic to oil is significantly more expensive than producing oil from conventional sources, which continues to offer more attractive profits to investors. However, the authors emphasize that the technology will be operated as a plastic waste management solution rather than an oil production alternative.
“While plastic-to-oil technology is not a silver bullet, its ability to generate value from waste makes it an important tool in the broader effort to tackle the global plastic crisis,” says Arboleda.
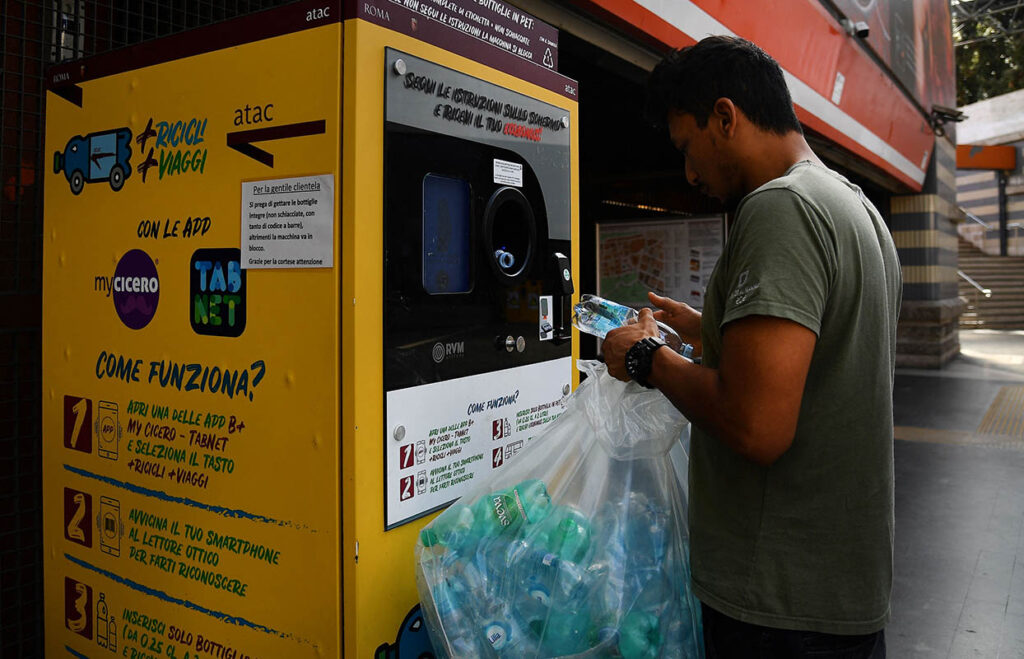
How much plastic could be converted to oil?
The authors—taking the significant challenges into account—use a conservative plastic-to-oil conversion rate of 70%. At this rate, the potential oil produced from plastic waste on a global scale is estimated at slightly over 1% of total global oil production—equivalent to 1.2 million barrels per day if all waste plastic were utilized.
A more realistic assumption places production at approximately 200,000 barrels per day under current conditions. However, by 2060, the amount could increase to 4 million barrels per day, depending on advancements in technology and their rate of adoption, factors that remain difficult to predict.
In Saudi Arabia, the authors estimate that plastic pyrolysis could initially produce over 12,000 barrels of oil per day, with the potential to reach some 124,000 barrels per day by 2060. While significant, this output remains small compared to the country’s overall oil production capacity.
Producers of plastic-to-oil technology are actively working to address the challenges posed by the cost, feedstock, and byproduct management. The authors believe that, as these issues are addressed, there will be substantial growth in the role of this technology in mitigating plastic waste, potentially becoming an important solution to this pressing global issue.
“It complements the broader goals of waste reduction and recycling in a circular economy, emphasizing its role in waste management rather than large-scale oil production,” concludes Arboleda.
Converting plastic to oil
The process of plastic-to-oil pyrolysis involves the thermal degradation of plastic in an inert atmosphere, breaking down the long-carbon chains in plastics into fuels like gasoline and diesel, along with some side products and impurities. To extract usable fuel, the resulting pyrolysis oil must be refined to separate it from unwanted substances. The pyrolysis process requires intense heat, operating at around 500°C.
The quality and type of fuel obtained depends on the nature of the plastic and its previous usage. However, even with high-quality plastic waste, the end-product still contains contaminants present in the original plastic that can cause corrosion, so requires further treatment before the oil can be used. This is done with purification and catalyst units that eliminate most contaminants from the synthetic fuel.
In addition, a purifier unit is needed to eliminate all the contaminants that were initially part of the plastic waste raw material. The purifier unit is usually installed before the catalytic reactor.
Reference
Arboleda, J.L. and Umeozor, E. Plastic to oil: Saudi Arabia and global perspectives. KAPSARC, 2023. | Article